Application Stories
Payout Calculations: Running with Clean Coolant Is a Major Cost Saving Initiative
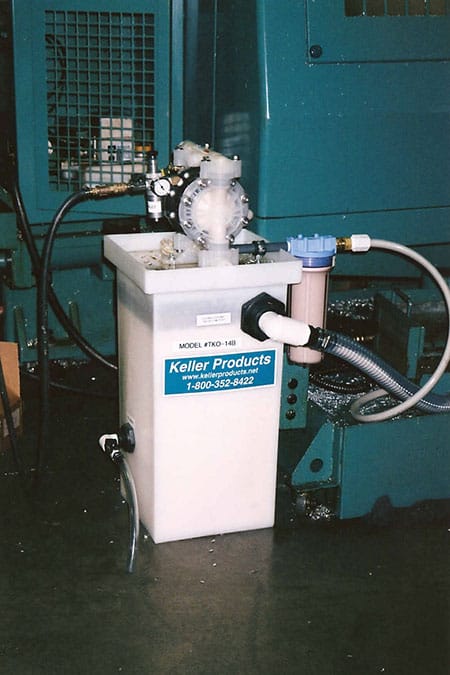
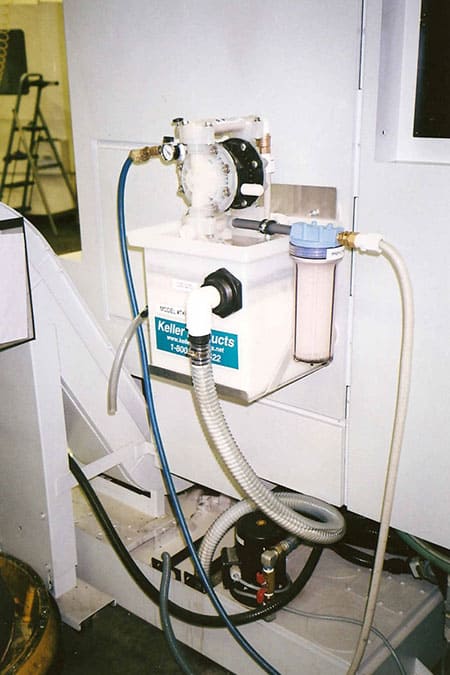
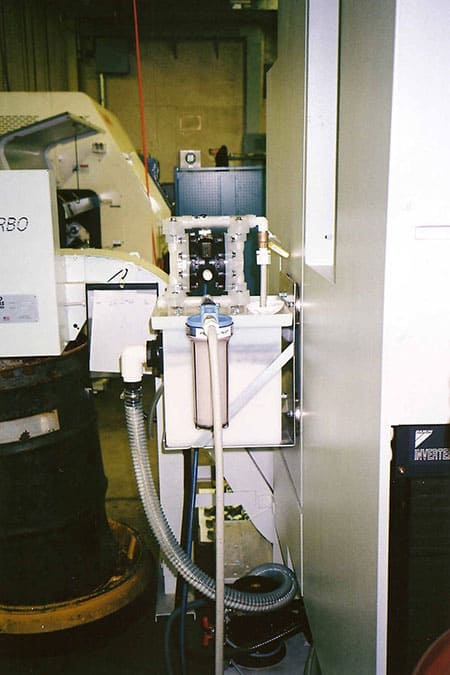
Until a few years ago, interest in maintaining the cleanliness of coolant in machine tool sumps arose chiefly from in-shop environmental concerns: odor was a problem, there was smoke in the air, or operators were suffering from contact dermatitis–all problems attributable to tramp oil in the coolant. However, while the environmental issues continue to be important, in the current difficult economy most shop managers recognize intuitively that maintaining clean coolant in the machines is essential for running an efficient and profitable shop. After all, if machine tools ran just as well with dirty coolant as with clean coolant no one would ever change coolant. However, despite the general agreement that clean coolant saves money, it is a rare shop manager who has actually calculated the cost savings resulting from maintaining clean coolant in the machines, and the savings are quite significant.
The cost savings result from the following improvements in shop operations:
- A good coolant maintained regularly with an efficient pump/skimmer unit can run at least one year in the sump before it should be changed. With no skimmer or with an inefficient belt or disc skimmer, the coolant must be changed every two months, or six times per year. Therefore, with efficient coolant maintenance, annual coolant purchase and disposal costs are reduced by five changeouts per year, or 83%.
- In addition, reducing coolant changeouts from six per year to one per year will similarly reduce by 83% the labor required for changing the coolant and the machine downtime during coolant changeouts.
- Running with clean coolant significantly reduces tool wear compared with running with dirty coolant. Based on feedback from hundreds of shops, a conservative estimate for the benefit of clean coolant is a 10% saving in tooling cost.
The following cost savings are calculated for one machine with an 80 gallon sump. The reduction in coolant changeouts will save five changeouts per year, or 400 gallons of coolant in the sump per year. The concentration of coolant makeup is assumed to be 5%.
Savings per Year | |||
---|---|---|---|
_ |
|||
Coolant Makeup: 5% of 400 gal.; or 20 gal. @ $20/gal. | $400 | ||
Coolant Disposal: 400 gal/year @ $2/gal. | $800 | ||
Labor for Changeouts: 4 man-hrs/changeout, 20 man-hrs/year @ $20/man-hr | $400 | ||
Machine Downtime: 20 machine-hrs/year @ $70/machine-hr | $1400 | ||
Tooling Cost: 10% savings of $10,000 tooling cost per machine/year | $1000 | ||
Total savings per machine per year: | $4000 | ||
_ |
|||
Approximate cost of pump/skimmer per sump | $1000 | ||
_ |
|||
Payback time for pump/skimmer: 0.25 years, or 3 months |
We can cite the example of PV Engineering (Salisbury MA) to illustrate the fact that cost savings and improved shop efficiency are now the driving forces in the decisions by shops to install efficient cooling cleaning equipment. PV Engineering, founded in 1988, is a family-owned shop serving the defense, power generation, and medical markets. They employ 21 CNC machines, primarily machining stainless steel. After analyzing his shop’s operation, Peter Vlismas, vice president of PV, concluded that ineffective coolant maintenance was having a detrimental effect on the performance of his shop. He contacted Keller Products, Inc., a leading supplier of coolant cleaning equipment, and cited the following specific objectives: “Minimize waste, run cleaner, and improve profits.” Since Keller has more than 5000 coolant cleaning units operating successfully in shops and the cost estimates suggest a potential saving by PV of more than $80,000 per year, the Keller salesman quickly reached an agreement with Peter Vlismas to initiate a test program. PV installed a TKO-14 pump/skimmer unit at the sump of one machine. In common with all Keller pump/skimmer units, the TKO-14 pulls oily coolant from the surface of the sump, filters to remove suspended solids, separates the tramp oil from the coolant with the patented Keller maintenance-free separator elements, and returns the cleaned coolant continuously to the sump at high flow rate. In contrast to the belt skimmers that PV had previously tried, a Keller pump/skimmer with a 1/2″ air-operated diaphragm pump turns over a sump rapidly-for example, a 90 gallon sump will be turned over twice per hour-aerating the coolant and ensuring that there are no stagnant areas of the sump in which oil and solids can accumulate. The separator may be run when the machine tool is operating or is idle.
After running the TKO-14 about one month, Peter Vlismas decided to equip his entire shop with Keller units. Keller supplies three models of TKO units to accomodate any shop space constraints. The TKO-14, which has a footprint of 14″ x 14″, could be conveniently set on the floor adjacent to seven of his 21 machines. For the remaining 14 machines, Peter selected the TKO-6 with the CLO-1 magnetic frame, which can be mounted off the floor directly to the machine tool and requires zero floor space. In operation, the TKO-6 performs exactly like the TKO-14. The Keller units have been operating for more than six months. The evaluation from Peter Vlismas: “Coolant waste has been greatly minimized, the machines run cleaner and more efficiently, and the shop is more profitable. The Keller units installed easily without interruption of shop operations. All my objectives for the program have been achieved at relatively low cost and with no operating problems.”
Conclusion: Maintaining clean coolant is an important Lean Manufacturing initiative.
New Pump/Skimmers Eliminate Dirty Coolant Bottleneck in Precision Machine Shop
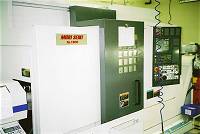
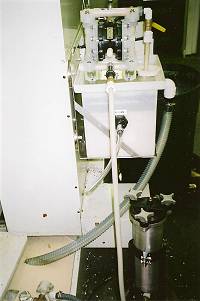
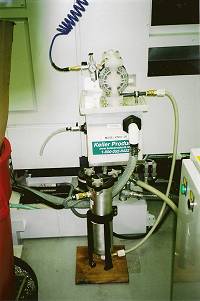
Stanfordville Machine (Stanfordville, NY), founded in 1975, is a leading supplier of precision parts to the semiconductor, medical, aerospace, and electronics industries. Running a busy shop with 24 machines, Stanfordville management continuously invests in new machines in order to ensure Just In Time deliveries and to be working with the latest in machine technology at all times. However, Peter Johnsen, Manufacturing Manager, found that his objectives for the long term investments in tools and tooling were being compromised by lack of effective maintenance of the coolant in his machine sumps. Buildup of tramp oil and other impurities in the coolant required frequent pumpouts of the sumps, resulting in excessive coolant and waste disposal costs and, more important, unacceptable unscheduled machine downtime.
Stanfordville Machine pursued some typical approaches for keeping the coolant clean. They tried skimmers with no success. A skimmer operates only in a small area of the sump, leaving most of the sump covered with oil, and removes a large quantity of coolant along with the tramp oil. They next tried a pumping separator with an electric pump. The electric pump immediately proved to be unreliable, and the overall construction of the separator was not rugged enough for the Stanfordville application.
Peter Johnsen then contacted Keller Products (Acton MA), which he knew to be a leader in coolant cleaning systems for sumps under 1000 gallons. With over 5000 units in the field, the rugged Keller pump/separators are specifically designed for trouble-free service, with 1/2” air-operated diaphragm pumps and patented permanent oil separating (coalescing) elements that require no maintenance. Keller offers both dedicated and portable units to handle any shop requirement. Since Peter did not want to require his crew to move portable units, the Keller salesman recommended the TKO line of pump/separators, designed to service individual sumps.
A TKO skimmer pumps oily coolant from a floating inlet device on the surface of the sump, through a prefilter to remove floating chips, and into a separator tank containing the Keller permanent separator element. The separated tramp oil is held in the tank until drained whenever convenient. The cleaned coolant recycles continuously to the sump at high flow rate. The high recirculation rate turns over the sump rapidly, ensuring that there are no stagnant areas in which oil and solids can accumulate. The smallest unit in the TKO line, the TKO-6, can be mounted to the side of the machine tool without hardware using the Keller magnetic support frame CLO-1. This feature was especially important to Peter, since it kept the aisleways clear for stock movement.
He ordered two TKO-6 units with magnetic frames and evaluated them for one month. They performed exceptionally well. Stanfordville primarily machines aluminum which generates a large quantity of floating fines that are pulled into the separator along with the tramp oil. Although the TKO separators are equipped with a cartridge type prefilter as standard, Peter requested that Keller supply the units with a high capacity bag filter for added operating convenience. Even including the bag filter and the 1/2” air operated pump, the Keller system was more economical than the unreliable pump separator previously evaluated.
The result of the test was total customer satisfaction. Peter Johnsen then ordered identical units for his remaining machines. He says, “I have cut my waste generation from 10 drums per month to two drums per month. In addition, I have increased production by minimizing downtime, which helps us meet our customer deadlines. By removing the tramp oil, my coolant is less likely to foam, and filtering out the aluminum means I am less likely to plug coolant lines in my machines. The Keller units paid for themselves in a few months. I’m glad I kept looking for the right solution to this difficult problem.”
Precision Valve Manufacturer Improves Productivity Dramatically with Model #315 Separators
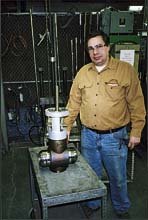
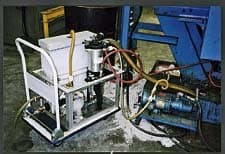
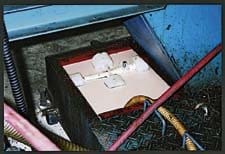
Conval, Inc. (Somers CT), founded in 1967, manufactures high pressure globe valves used primarily in the power generating industry. The fact that Conval exports about 76% of its output is testimony to the worldwide reputation for quality and reliability its valves have achieved in this extremely demanding service. The valve bodies are machined from forgings, primarily steel plus some aluminum, bronze, and Stellite, on 20 CNC machines operating two shifts. Because the shop has been extremely busy over an extended period of time, Roger Poirier, shop manager, is constantly evaluating all areas of shop operation to find possible gains in productivity.
One source of continuing production problems was contamination of the coolant. High levels of tramp oil and solids in the coolant flooding the working part caused rapid tool wear. According to Roger, “The rapid tool wear required frequent machine adjustments during a run in order to maintain Conval’s tight dimensional specifications. Even with these adjustments, the amount of rework on out-ofspecification parts was bogging down our delivery schedules. In addition, we were pumping out and changing our sumps every six weeks.” The reduced throughput on the machines and the loss of machine time for pumpout convinced Poirier that he had to act to deal with the coolant contamination problem.
Roger was referred to Keller Products, Inc. (Acton, MA) by his coolant supplier. Keller Products is a leader in sump-side coolant cleaners, with thousands of units in service. The Keller salesman surveyed the shop and quickly determined that one of Keller’s five standard portable pump/separator units, Model #315, could be recommended to solve the Conval coolant contamination problem. The cart-mounted Model #315 pump/separator unit can clean a typical 60 gallon to 200 gallon sump in a few hours and then can be easily moved and set up at the next sump. Keller recommends that each sump be treated once per week. Since the Model #315 can readily treat two sumps in an 8 hour shift, one separator can maintain the cleanliness of the coolant in 10 or more sumps. All Keller separators incorporate self-priming air operated pumps (no electricals), a bag filter to remove floating solids that enter the separator with the oily coolant, and patented permanent oil separator elements.
Roger Poirier purchased one Model #315, and the results were dramatic. He states, “On the first couple of machines, we removed 2 to 3 gallons of tramp oil in a few hours. The bag filter removes the fines associated with machining forged material. We are currently going on nine months with coolant in the sump, and there is no indication yet that the coolant will need to be changed any time soon. Tool life has increased substantially, the need to make machine adjustments during a run has dropped sharply, and rework due to coolant issues has been virtually eliminated. Not to mention the savings associated with eliminating downtine and disposal of coolant for pumping out 20 CNC machines every six weeks.” About one month after installing the first Model #315, Poirier purchased a second unit to ensure that all 20 Conval sumps will be kept free of tramp oil and floating solids. Noting that the dramatic improvements in shop operations were achieved with the modest investment in the Keller units and without interrupting normal operating procedures, Poirier says his only regret is that he did not address the coolant problems sooner.
Two Keller Model #455 Tramp Oil Separators Keep Sumps of 20 CNC Machines Clean
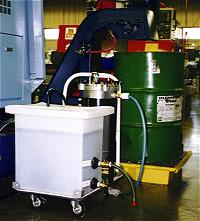
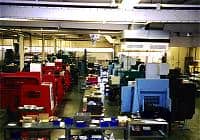
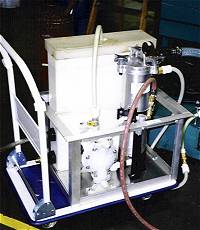
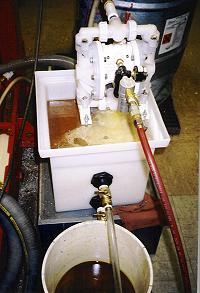
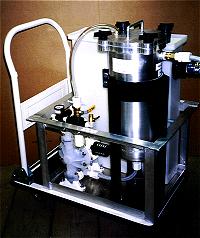
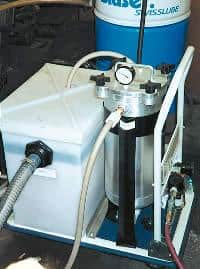
Well before “Lean Manufacturing” had become the standard term for efficient manufacturing, Stevens Manufacturing Co. (Milford CT), a supplier of precision parts to the aerospace aftermarket, was implementing the principles of lean manufacturing with its on-going process improvement programs. In fact, Steve Fogler Jr., shop manager, credits Stevens’ success in maintaining its competitive position during difficult times to its emphasis on continually upgrading the processes.
One aspect of the operation to which Steve has devoted continuing attention is maintenance of the coolant. Stevens runs 20 CNC machines, none older than 10 years, cutting everything from plastics to steel to titanium in relatively short production runs. Their customers, such as Boeing, Sikorsky, and the U. S. government, set extremely tight dimensional and surface finish specifications. Tramp oil and other contaminants in coolant greatly increase the difficulty in meeting the tight specifications. High levels of tramp oil in coolant cause accelerated tool wear, degradation of parts finish, and the requirement to adjust machine settings frequently to achieve the dimensional specifications. In addition, tramp oil in the coolant generates smoke in the shop, plus odor and the potential for operator dermatitis as a consequence of bacteria attack on the oil. Also, when cutting relatively low density materials such as plastics and titanium, the chips which remain suspended in the coolant are picked up by the coolant pump and sprayed onto the working part, compromising the surface finish. In order to maintain product quality and achieve production targets, Stevens was dumping coolant and recharging with new coolant every three months. The cost was substantial––not only the cost of new coolant and disposing of about 100 gallons of spent coolant for each of 20 machines every three months, but also the roughly four hours of labor per machine to drain and clean the sump, and replenish the coolant. In addition, each machine is down during coolant changeover.
Steve Fogler recognized that the coolant problem had to be solved in order to improve shop efficiency and reduce costs. It was clear that belt or disc skimmers, a conventional method for removing tramp oil from sumps, would not address the Stevens requirements, because a skimmer does not create circulation in a sump and therefore is ineffective on larger sumps, and a skimmer does not reduce the quantity of solids suspended in the coolant. To improve the situation significantly, Stevens required a coolant purifier which would separate tramp oil efficiently, recirculate the coolant at high rate even when the machine tool is idle, and filter to remove suspended chips.
In 1998, Stevens purchased a coolant purifier supplied by Keller Products, Inc. (Lexington MA), which met all these requirements. With the new purifier, coolant life was immediately extended from 3 months to one year. After recently adding several new machining centers, Stevens purchased a second Keller coolant purifier, the Model #455 Separator. Steve Fogler says, “The money saved on hauling waste coolant and buying new coolant by greatly extending the coolant life is only a small part of the savings. The biggest saving is in the labor and downtime to dump, clean, and recharge the sumps of 20 machines every three months.”
A Keller coolant purifier operates by pulling oily coolant from the surface of the sump via a compact inlet device and then through a high capacity bag filter to remove suspended solids. The coolant/tramp oil mixture, free of solids, is pumped through the patented Keller oil separator elements, which are immersed in a plastic tank. The permanent oil separator elements, constructed from stacks of plastic discs with fine flow passages, efficiently split oil from coolant at high flow velocity, creating the opportunity to design high flow rate separators in compact packages. The cleaned coolant is continuously returned to the sump, and the tramp oil collected in the separator tank is drained to a waste oil container periodically, usually once per day. A sump typically can be cleaned in a few hours, and then the pump/separator can be easily moved to another sump and set up to run in about five minutes. The Keller separator, which requires only a 1/4-inch compressed air line for operation, can be run while the machine tool is operating or when shut down.
Despite the fact that the Model #455 is the largest separator in the Keller line, capable of treating individual sumps up to 1000 gallons, it requires only 20” x 30” of floor space and is easily portable. With a coolant recirculation rate of 180 gallons per hour, a Model #455 can clean a 100 gallon sump in less than two hours. Steve Fogler says, “I can easily cover the whole shop with the two Keller units. I run for about one or two hours every other week on each sump, and the coolant looks like swimming pool water.” The resulting operating benefits are: improved machine efficiency, extended tool life, better parts finish, and greatly reduced machine downtime. Another advantage to operating with clean coolant, obvious to any visitor, is the overall cleanliness of the Stevens shop and the absence of smoke in the air which can be caused by tramp oil in the coolant.
Steve Fogler says, “To stay competitive, I have to stay lean, and to me lean means minimizing time spent on non-value-added projects. Lean isn’t about not spending money, and it is not always about exotic new machines or programs. Sometimes lean is just making sure your existing assets are operating at maximum efficiency. Our coolant maintenance system is an important element in our on-going program to maximize operating efficiency.”
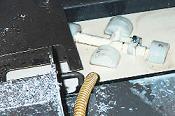
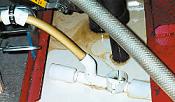
Portable Pump/Filter Unit Helps Precision Machine Shop Cut Costs Dramatically
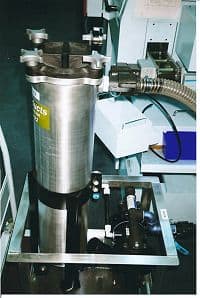
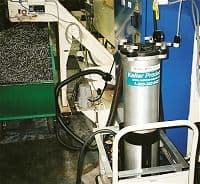
Hayn Enterprises, LLC (Rocky Hill CT), established in 1960, is a leading manufacturer of turnbuckles and cable hardware for the marine and architectural industries. Primarily machining type 316 stainless steel exclusively, they utilize 8 Swiss CNC machines, an Okuma mill, two CNC turret lathes, and a Mazak mill, all machining with cutting oil. Hayn engineers found that the condition of the cutting oil was contributing to some difficult quality and production problems.
According to Ted Beger, supervisor of the machine shop, fragments from the machining process were accumulating in the oil, and the these fragments were embedding in the 316SS during various machining operations. The result was thread galling and parts rusting. In addition, the fragments in the cutting oil were in turn accelerating the wear on the tooling, leading to poor tooling life and abbreviated filter life in the bag filters on the high pressure coolant systems.
While researching possible solutions to the problem of contaminants in the cutting oil, Hayn engineers visited a trade show exhibit of products by Keller Products, Inc. Keller supplies complete lines of equipment for filtering and purifying cutting oil and water-base coolant. The particular Keller unit of interest to the Hayn engineers was the PFA-1002, a portable pump/filter unit which is designed to remove solids from cutting oil or coolant in machine tool sumps without the need to pump out or shovel out the sumps. The PFA-1002 pump/filter unit contains a rugged, high flow rate air-operated diaphragm pump and a high capacity bag filter which removes solids as fine as 1 micron, mounted in a frame on a compact cart. With a recirculation rate of 20 gallons per minute, the PFA-1002 completely cleans fines and chips from a typical sump in minutes, and then is easily moved to another sump and set up to run simply by connecting a 1/4″ compressed air line. With no electricals, the unit is inherently fireproof. The self-priming pump pulls the cutting oil from the sump through a large diameter vacuum hose into the bag filter and continuously pumps the filtered liquid back to the sump at high flow velocity. The force of the filtered liquid discharge scours the bottom of the sump and keeps chips and fines suspended in the oil for pickup by the inlet hose. Because the oil is not drained from the sump during the brief cleaning operation, the machine tool need not be taken offline for solids removal. Routine maintenance on the pump/filter unit consists of changing or emptying the filter bag when the pumping rate slows. In many applications, the filter bag may be emptied and reused a number of times.
The Hayn engineers purchased one PFA-1002 to service all twelve machines in the shop. Ted Beger reports that with the PFA-1002 in service tooling life has improved by 40 to 50 percent. The galling and rusting problems have been virtually eliminated so that they now have no scrap due to contaminated cutting oils. The filter bag life in the high pressure systems has tripled. He says that all these improvements were obtained at relatively low pump/filter unit operating. Ted Beger says, ‘The PFA-1002 was a low cost and convenient solution to difficult and expensive quality and production problems. I would recommend this product to anyone doing precision machine work with straight oil.”
Portable Pump/Filter Unit Takes Chips from Cutting Oil to Improve Efficiency of Swiss Screw Machine Shop
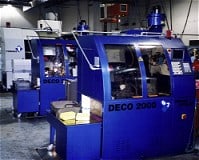
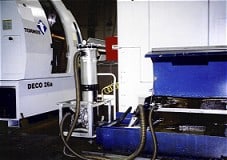
CSI Manufacturing, Southboro, MA, is a Swiss CNC screw machine shop specializing in high precision components for fluid controls, aerospace, weapons, and telecommunication devices, fabricated from a variety of metals, including steel, brass, and aluminum. CSI, a partner in a group of eight companies in New England and Europe offering one source turning solutions, operates 16 CNC machines 20+ hours per day, 7 days per week. Steve Doody, President and founder of CSI, says that the intensive production schedule, while desirable for the health of the business, presented him with some nagging operating problems. Because of the volume of relatively small parts running steadily in the machines, the concentration of small chips and fines in the oil increased rapidly to interfere with machine performance. The small chips were entering the gundrills, causing tool breakage and loss of finish on parts, leading to unacceptable reject rates and unscheduled machine stoppages. The resulting cleaning of the machines led to further downtime and also put additional burdens on the housekeeping crew, since Steve prides himself on a clean and orderly shop.
Steve discussed the problem of solids buildup in the oil with his Swiss machine supplier. The supplier knew that customers had successfully addressed similar problems using the Keller Products PFA-1002 pump/filter unit and recommended that Steve contact Keller. The PFA-1002 can clean suspended solids and settled sludge from a sump in about 30 minutes or less, without the need to pump out the machine tool. It contains a high capacity bag filter to filter as fine as 5 microns and a pump which recycles up to 20 gallons per minute of clean oil to the sump. Since the pump is driven by compressed air and there are no electrical components, the system is inherently fireproof, an important benefit when processing straight oils. Mounted on a 20″ x 30″ cart, the easily portable PFA-1002 is wheeled to the side of the sump, the inlet and outlet hoses are positioned in the sump, and a shop 1/4” compressed air line is connected. Setting up at a sump requires about 5 minutes. The dirty oil is pulled from the sump through the 1 1/2″ inlet hose, filtered by the bag filter, and continuously returned to the sump. The force of the clean discharge can be used to scour the bottom of the sump to resuspend settled solids for pickup by the inlet line. The sump is never emptied, and the machine tool can run for extended periods without additional maintenance.
Steve Doody purchased one PFA-1002, and he reported that the problems he was having with solids in the sumps were virtually eliminated. CSI operates the PFA-1002 for a few hours every day to clean each of the 16 sumps about once per week. As a result of this simple and inexpensive cleaning schedule, Steve Doody says, “Machines can complete their scheduled runs unattended, quality problems have been eliminated, and tool life is greatly extended. Our production efficiency is much improved because we no longer have to shut machines down to service the sumps. In addition to these quantifiable improvements, the operators appreciate the elimination of a very unpopular task, and I appreciate the fact that we have less oil to clean off the shop floor.”
Steve Doody was pleased to learn of an additional application for which the PFA-1002 is well suited. He found he could use the portable pump/filter to remove suspended solids from the oil reclaimed from the chip spinner, which is typically loaded with fines. The self-priming pump on the PFA-1002 allows Steve to pump the filtered oil from the chip spinning process into a 55-gallon drum, which he then moves through the shop to top off machines with oil as needed.
With the number of machine tools in service at CSI and the versatility demonstrated by the Keller PFA-1002, Steve Doody purchased a second unit to ensure that his shop maintenance needs are being met. To summarize the impact of the PFA-1002 on his shop, Steve says, “In my opinion, this is the perfect example of the application of Lean Manufacturing initiatives––specifically, the elimination of non-value-added time. My shop was built on the concept of being able to produce parts automatically, only to be challenged by solids buildup in the oil. Then, for a modest investment (about $2,500 each), the two PFA-1002 units have allowed me to increase shop throughput, avoid unscheduled shutdowns, eliminate several problems relating to part finishes, greatly reduce labor costs associated with sump maintenance, and improve overall shop cleanliness and working conditions. Considering the investment in top-line CNC machines, tooling, and producing the part itself, ensuring that we run with clean oil just made sense.”
Problem of Solids Buildup in Sumps Solved for Specialty Machine Shop
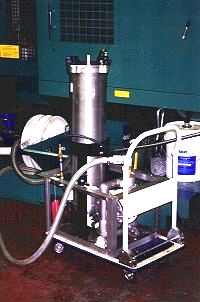
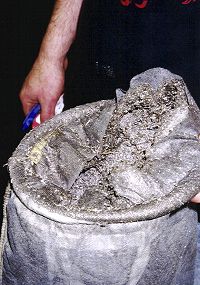
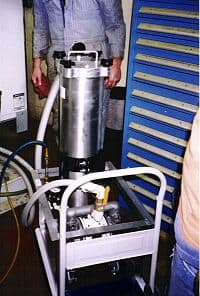
Bradford Machine Co. (Brattleboro VT), a precision specialty shop making medical components and other close-tolerance products, faced a time-consuming and expensive problem with buildup of chips and sludge in the sumps of the machines. Bradford operates 14 CNC’s, 6 mills, 5 lathes, and 3 EDM machines, cutting primarily aluminum and exotic steels. John Therrien, shop manager, says, “On the milling machines, chip buildup in the coolant caused the pump to clog and cut off coolant flow. Also, chips packing in the sump could result in coolant overflow onto the floor. On the smaller sumps, it takes four hours to pump out the coolant, shovel muck from the bottom of the sump, wipe down the machine, and pump back fresh coolant. On the large mill it’s an eight hour project. Since the mills are operated two shifts, five days per week, shutting down for 4 to 8 hours for a complete cleanout was done only when absolutely necessary. On the lathes, the buildup of fines in the coolant adversely affected the surface finish and required replacing the coolant every few months. Plus, the cost of waste disposal is constantly increasing.”
Therrien’s objective was to find a method for cleaning out the solids without the need for shoveling out the sumps. He tested an air-driven vacuum head fitted on a 55 gallon drum. Although the device removed the coolant from the sump, it left behind a considerable quantity of solids in the corners of the sump. In addition, it used so much compressed air that the air pressure at the machines fell below the low pressure alarm level. Therrien also considered a large portable filter and vacuum tank system, but decided that it would be impractical in the tight spaces of his shop. The problem of buildup of solids in the sumps remained unsolved until Therrien learned that Keller Products, Inc. (Lexington, MA), who previously supplied an efficient tramp oil separator to Bradford, had introduced a new pump/filter unit, PFA-1002, which looked promising as a practical solution to the problem.
The PFA-1002 incorporates a high capacity bag filter and a high flow rate air-operated diaphragm pump, mounted on a compact (20” x 30”) cart. The mixture of coolant and solids is pulled through a large diameter inlet hose into the bag filter, which removes all solids as fine as 5 microns. The filtered coolant is returned to the sump under pump pressure at 20 gallons per minute. The force of the pressurized liquid discharge scours the bottom of the sump and keeps chips and sludge suspended in the sump for pickup by the inlet hose. The PFA-1002 can clean settled and suspended solids from a typical sump in 15 to 30 minutes. The machine tool is shut down during the brief cleaning period, but there is no need to take it off line, in contrast to the 4 to 8 hours of machine downtime required to pump the sump dry and shovel out the solids. With only a 1/4-inch compressed air line connection (no electricals), the cart-mounted PFA–1002 may be moved to another sump and set up to operate in minutes. The only maintenance required is to empty or change the filter bag when the pumping rate slows. When filtering relatively dry solids, such as aluminum chips, the filter bag may be emptied and reused multiple times. A new filter bag costs $7.00. Bradford is using water soluble coolants, but the PFA-1002 is equally effective removing solids from cutting oils.
Bradford has been using the Keller PFA-1002 to maintain the sumps in all the mills and lathes since last year. John says, “We now clean each of the sumps in rotation as needed, usually once in three or four weeks, during scheduled Friday afternoon maintenance. We can do a quick cleaning in 15 minutes, or a more complete cleaning in about 30 minutes by pulling the conveyor. The cleaning operation is usually a one man job.” Because there is essentially no holdup volume in the PFA-1002, the unit may be rotated among different coolants without mixing. John Therrien has concluded, “The use of the PFA-1002 has eliminated machine inefficiencies caused by excessive solids in the coolant, eliminated unscheduled machine downtime for sump cleanouts, greatly reduced the man hours devoted to coolant maintenance, and completely eliminated the unpopular task of shoveling solids from the sumps.” Needless to say, both shop management and shop operators are very pleased with the performance of the PFA-1002.
High Precision Shop Solves the Problem of Solids Buildup in Screw Machine Cutting Oil with Portable Pump/Filter Unit
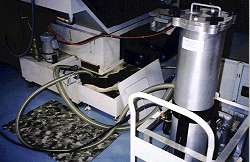
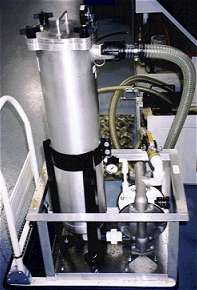
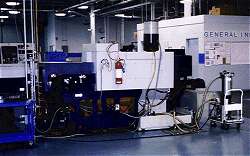
Marox Corporation (Holyoke, MA) is a contract manufacturer specializing in high precision machining of implants, external fixations, and surgical instruments for the medical industry, plus components with demanding specifications for the aerospace industry. Having celebrated its 50th year in business last year, Marox has 65 employees running two full shifts, 7 days per week, in a modern facility built in 2000. Brian Rosenkranz, Vice President, attributes Marox’s success to their decision to stay at the cutting edge of manufacturing technology. They utilize up-to-date concepts such as lean manufacturing and high-tech integrated computer systems. To ensure total quality control, Marox performs most operations in house and jobs out very little. Their products are manufactured from stainless steel, titanium, aluminum, and other specialty metals and polymers on modern CNC equipment, such as palletized horizontal machining centers, five-axis vertical machining centers, and up to twelve-axis swiss type screw machines. Because Marox’s customers rely on their “Dock-to-Stock” deliveries, down-time of machines is not an option for them. Marox makes a point of maintaining an exceptionally clean shop to demonstrate both to their customers and their employees that meticulous work and total attention to cleanliness are essential elements of their products. In fact, Brian Rosenkranz likes to say that his customers would not feel out of place coming from an operating room into his shop.
Marox has 9 new CNC screw machines which utilize cutting oil as the working fluid and 15 CNC millers with water-base coolant. Buildup of solids in the cutting oil in the screw machines was causing major problems in shop housekeeping, obviously a serious concern for Marox, as well as generating significant costs for unproductive labor and machine downtime. As described by Michael Consolmagno, Vice President of the Marox CNC Turning Unit, the problems caused by buildup of solids in the sumps of the screw machines, particularly critical with the new design machines, are:
- Chips and fines plug the coolant pump inlet screens, causing the low flow alarm to shut down the machine.
- A high concentration of fines in the coolant loop compromises the finish on precision parts.
- When the high pressure coolant pump is utilized, about 20% of the time, solids rapidly plug the filters in the high pressure loop, requiring frequent machine shutdowns to change the filter bag.
Until recently, the only solution that Marox had to the problem of excessive solids in the oil was to shut down the machine and manually rake and shovel the solids from the sump. The economic costs for this non-productive (and unpopular) function are the machine downtime and the use of skilled labor. Even in the new screw machines, the sumps are not readily accessible for solids raking or shoveling. Mike Consolmagno estimates three hours of machine downtime and labor to clean one sump. In addition to the economic costs, the manual sump cleaning and chip handling unavoidably produced oily deposits that challenged the Marox scrupulous housekeeping program.
The problem of solids buildup in the sumps was solved literally overnight when the salesman from Keller Products, Inc. (Lexington, MA) introduced to Mike Consolmagno the new portable pump/filter unit PFA-1002. The Keller PFA-1002 can clean settled and suspended solids from a sump without the need to drain the sump or shovel the solids. The PFA-1002 contains a high capacity bag filter and a high flow rate air-operated pump, mounted on a compact (20” x 30”) cart. With the inlet and outlet hoses inserted in the sump, the mixture of solids and oil is pulled into the bag filter, which removes all solids as fine as 5 microns, and the filtered oil is continuously returned to the sump under pump pressure at 20 gallons per minute. The force of the pressurized liquid discharge scours the bottom of the sump and keeps chips and sludge suspended in the sump for pickup by the inlet hose. The PFA-1002 can clean settled and suspended solids from a typical sump in 60 minutes or less. Requiring only a 1/4” compressed air line for operation (no electricals), the cart mounted pump/filter unit can be moved to another sump and set up to run in minutes. The only maintenance required is to empty or change the filter bag when the pumping rate slows or stops. Replacement filter bags cost $7.00 each. The self-priming diaphragm pump has a suction lift of 15 feet and can be run dry or dead-ended without damage.
Marox now utilizes one PFA-1002 to service all nine CNC screw machines. Mike Consolmagno says that treating each sump with the pump/filter unit for about one hour each week eliminates the screen plugging and parts finish problems associated with solids buildup in the sumps, and at the same time completely eliminates the messy and time consuming pump-out and shoveling operations. Now the machine tool is not taken off line for the sump cleaning. Since Marox uses two types of cutting oil, Mike particularly likes the feature that the self-priming pump on the PFA-1002 completely drains the bag filter on the separator after a sump is treated so that the next sump can be treated without mixing oils. He also points out that although on many of the machines access to the sumps is severely limited, the 8 foot lengths of both the inlet and outlet hoses and the fact that the pump on the PFA-1002 is self-priming permit quickly setting up and operating the unit on even the most difficult sumps, without significant sump modifications.
Marox also uses the PFA-1002 to reduce the solids load on the high pressure filter when the high pressure oil pump is operating. The PFA-1002 is set up with the inlet hose positioned in the sump remote from the high pressure pump inlet and the outlet hose discharges filtered oil into the vicinity of the pump inlet. With the PFA-1002 operating in conjunction with the high pressure pump, the solids load in the high pressure pumping circuit is greatly reduced, and the time between bag changes on the high pressure filter is significantly increased.
To sum up the benefits of the Keller unit, Mike Consolmagno says, “The PFA-1002 is rugged and easy to use. It works exactly as described, with negligible operating cost, and it has eliminated several costly problems. No more pumping out and shoveling out sumps, no more problems of fines affecting parts finishes, no more short runs with the high pressure coolant filter, and with one PFA-1002 it is far easier for us to maintain our high standards of housekeeping in the entire shop.”
Medical Instrument Manufacturer Elminates Difficult Coolant Line Plugging Problem with Simple Filtration Solution
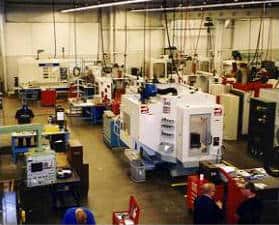
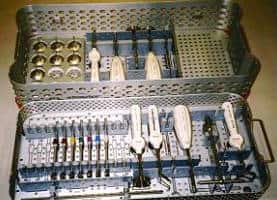
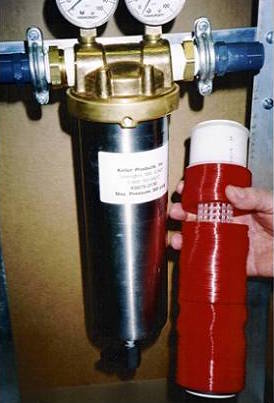
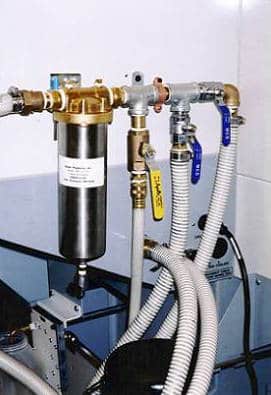
A Massachusetts manufacturer of complete operating room packs meets the strictest medical instrument specifications by performing in-house all operations necessary to deliver procedure packs “ready for the operating room.” To achieve total in-house control over all operations, the manufacturer machines the raw stock, does laser welding as required, labels the instruments, manufactures the instrument packages, and assembles the instruments in the procedure packs. This approach to the market requires developing a diverse range of manufacturing expertise and capabilities, and also demands the ability to make quick changes on the fly throughout the process whenever a customer changes delivery schedules or product requirements.
To stay abreast of this dynamic production situation, they run a two shift 20 hour operation, and lost production time is not tolerable. Unfortunately, they experienced frequent unscheduled machine downtime as a result of plugging in the coolant delivery lines of two new vertical machining centers, which are equipped with 3/4” to 1/4” lines to feed the through-the-spindle coolant and five coolant nozzles. Loss of coolant flow automatically shuts down the machines, which often run unattended. The coolant line plugging problem was particularly troublesome when machining titanium because the light titanium fines, which float in the sump, are picked up by the coolant pump and pumped into the spindle and coolant nozzle lines. Maintenance found that about every two weeks the fines would pack into the coolant delivery lines and back up 12” from the discharge nozzles and spindle. It was then necessary to shut down the machine, pull off all the nozzles and bellows covers and clean the lines. This operation is performed by a man in a cramped space in the machine for 3 to 4 hours, obviously not a popular job for the machine operator. More important for management, each of the two machine tools was off-line for 3 to 4 hours every two weeks, when every production hour was urgently needed.
The shop maintenance supervisor recognized that it should be possible to alleviate or even eliminate the plugging problem by filtering out the solids downstream from the pump, before the line splits into the coolant distribution manifold. Since he was quite satisfied with the performance of two portable pump/separator units to remove tramp oil from the coolant he had previously purchased from Keller Products (Acton MA), he decided to contact Keller for a possible solution to the coolant line plugging problem. The Keller salesman immediately recommended the Model XS075–2130 stainless steel and brass filter housing containing a 100 micron Keller permanent cleanable filter element. The rugged housing, about 4” diameter by 14” high with 3/4” inlet and outlet ports, is easily installed by the shop in the coolant delivery line. The Keller proprietary permanent filter element, which fits all standard cartridge filter housings, has a much higher flow rate at low pressure drop than a similar size disposable filter element. The cleanable filter element is constructed of thin plastic discs with precisely sized grooves, mounted on a plastic core. The large internal filter surface area provides excellent solids holding capacity and long runs between cleanings. When cleaning is required, the element is removed from the housing, and the discs separate to a stop on the core. The all-plastic element can then be cleaned in a bucket of water, by washing with a hose, or in a parts cleaner. Any shop cleaning agent or solvent can be used. The Keller filters with permanent elements, available in ratings from 40 mesh to 300 mesh (50 micron) and flow rates to 150 gallons per minute, are ideal for any through-the-spindle or through-the-tool applications.
The XS075–2130 assemblies were installed in the coolant line on each of the two machines. A spare cleanable filter element was purchased for each filter housing. The result: the coolant line plugging problems have completely disappeared, the 3 to 4 hours of unscheduled downtime per machine every two weeks have been eliminated, and the machines can run unattended without danger of shutdown because of loss of coolant flow. The only filter maintenance required is to remove the dirty filter element and replace it with the clean standby element once every two weeks, a task of about 5 minutes. The dirty element is then cleaned and stored for the next cycle. The maintenance supervisor says, “The Keller filters completely eliminated unacceptable machine downtime, and the machines are now running at maximum productivity. The filters are relatively inexpensive and were easy to install. The Keller filters are a simple solution to a difficult production problem.”
Reprinted from MAN/MODERN APPLICATIONS NEWS, April 2002
Pump/Separator for Coolant Management Viewed as Production Enhancement Tool
Clean coolant can produce benefits well beyond the traditional "environmental" issues, especially with large sumps and high-pressure systems.
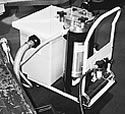
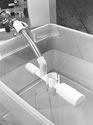
The elimination of “Monday morning odor,” reducing coolant waste, and improving in-shop working conditions are frequently sufficient reasons for installation of coolant cleaning equipment and coolant management programs. However, Jonathan Strauss, sales manager, Keller Products, Inc. (Lexington, MA), maintains there are major production and profit benefits that also may be gained.
“Three of the most expensive items in the shop are the machining centers, the tooling, and the part they are cutting; and the coolant is in contact with all three,” advises Strauss. He adds that in-shop experience has shown that degradation of the coolant will result in abbreviated tool life, poor parts finish, excessive downtime for machine maintenance, and frequent coolant pump-out. “Relatively low-cost coolant cleaning equipment can address all these problems,” says Strauss.
As shops invest in high-pressure coolant systems and through-the-spindle cooling, it is more important to view coolant-cleaning equipment as an aid to productivity, because clean coolant is less likely to foam in these applications.
For small sumps, belt- and disc-type skimmers adequately perform the task of tramp oil removal. However for large sumps or sumps with heavy loads of tramp oil or solids, a pump/separator unit that incorporates a filter may provide additional benefits. A pump/separator unit continuously recirculates the coolant filtering suspended solids and separating tramp oil. A typical unit consists of an inlet device positioned in the sump to pull oily coolant primarily from the sump surface, a prefilter for solids removal, an air-operated diaphragm pump, and a tramp oil separation sec- tion. A unit like this may be run when the machine tool is operating or shut-down.
Pump/separator units may be permanently installed to serve a single large sump, or a portable unit may be rotated among several machine sumps to clean each sump at least once a week. A single portable unit capable of serving multiple machines makes the coolant cleaning investment more attractive for many shops.
Coolant Test
The first step in se-lecting a pump/separator unit, explains Strauss, is to determine the oil rejection properties of the coolant being used. “The better a coolant rejects oil, the easier it is to keep clean and the longer it can be maintained in the sump,” he notes. “A fresh coolant with good oil rejection characteristics will readily split-out the tramp oil (or way oil) to the surface of the sump, if the coolant is allowed to stand for 30 minutes.”
30 April 2002 www.modernapplicationsnews.com
A floating inlet device pulls oily coolant into the separator from the sump surface and automatically compensates for changes in sump liquid level. When aluminum is being machined, the inlet device and separator unit must be capable of handling a large quantity of suspended solids.
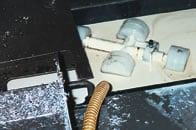
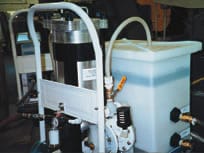
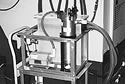
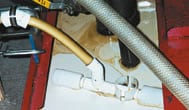
A simple field-test of the condition of the coolant is to take a sample of the coolant from the sump while it is running and allow the sample to stand for 30 minutes. Oil that separates to the top of this sample will be removed by an efficient pump/separator unit. Only a fraction of the oil that remains dispersed or emulsified in the bulk of the coolant after 30 minutes will be removed by a pump/separator or a skimmer unit.
Because the oil rejection ability of any coolant diminishes over time, a good recommendation is to select a separator specifically designed to work with slow-separating coolants. “Rather that trying to reclaim spent coolants,” suggests Strauss, “the better approach is to start with fresh coolant and maintain it properly.”
The size of the circulating pump on a separator is determined by the size of the sump. For sumps up to about 100 gal., a unit with a recir-culation rate of 60 gal./hr. should be sufficient. Larger sumps may require units capable of 120 gal./hr.
The materials being machined also have a major impact on the type of separator to be used. “If the shop machines more than 25% combined of materials that produce a large quantity of suspended solids, such as aluminum, cast iron, brass, copper, plastics, and titanium, the pump/ separator unit should be equipped with a high-capacity pre-filter, usually a bag filter, to protect the pump on the separator and prevent build-up of sludge in the oil separation section,” says Strauss.
By viewing coolant management as a production enhancer, rather than solely an environmental improvement option, shops can more accurately gauge whether this approach is cost-justified.
“A regular coolant management pro-gram can greatly increase tool life, improve parts finish, reduce downtime due to untimely pump-outs, and improve the overall condition of the machining center,” stresses Strauss. Keller Products, Inc.
Portable Pump/Filter Unit Solves Difficult and Costly Problems for Precision Machine Shop
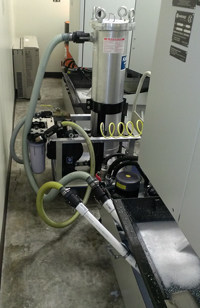
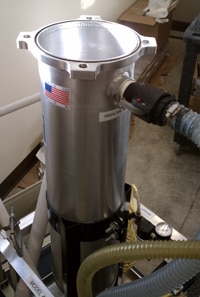
Brooks Precision Machining Inc., a rapidly growing New England shop specializing in aluminum sub-assemblies and complex components for a variety of industries, was faced with the problem of buildup of aluminum fines in the machine sumps. The fines buildup was limiting coolant life and required frequent stoppages to clean out the sumps. Eric Brooks, Operations Manager, assumed responsibility for solving the problem. An inquiry to a local distributor led Eric to Keller Products Inc. (Acton MA). Keller Products specializes in filtration and separation solutions designed to keep coolant as clean as possible for as long as possible in the machine sumps. A quick review of the situation led Keller to recommend the portable pumpffilter system Model PFA-1002.
The PFA-1002 pump filter unit contains a rugged, high flow rate air-operated diaphragm pump and a high capacity bag filter which removes solids as fine as 1 micron, mounted on a compact cart. With a recirculation rate of 20 gallons per minute, the PFA-1AO2 completely cleans fines and chips from a typical sump in minutes, and then is easily moved to another sump and set up to run simply by connecting a ¼” compressed air iine. With no electricals, the unit is inherently explosion-proof. The self-priming pump pulls the coolant from the sump through a large diameter vacuum hose into the bag filter, and continuously pumps the filtered liquid back to the sump at high velocity. The force of the filtered liquid discharge scours the bottom of the sump and keeps chips and fines suspended in the coolant for pickup by the inlet hose. Because the coolant is not drained from the sump during the brief cleaning operation, the machine tool need not be taken offline for solids removal, thus minimizing downtime. Routine maintenance on the pump filter unit consists of changing or emptying the filter bag when the pumping rate slows. In many applications, particularly when filtering aluminum, the filter hag may be emptied and reused a number of times.
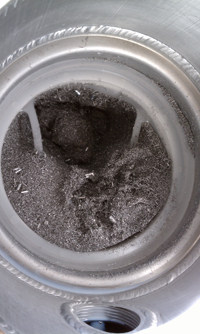
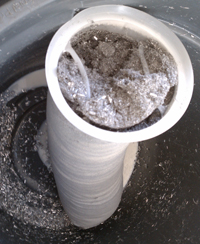
Brooks purchased one PFA-1002 to service all 16 machines in the shop. Eric Brooks reports that with the PFA-1002 the requirement to pump out the machine sumps has been completely eliminated. The reduction in downtime and labor and the corresponding increase in productivity has allowed Brooks to maintain on-time deliveries even during their dramatic growth. Eric says that these improvements were obtained at the relatively low cost of the pump filter unit. He says, “The PFA-1002 was an inexpensive and convenient solution to difficult and costly production problems. I would recommend this product to anyone doing precision machine work on aluminum parts.”
Portable Pump/Filter Unit Solves Difficult and Costly Problems for Precision Machine Shop
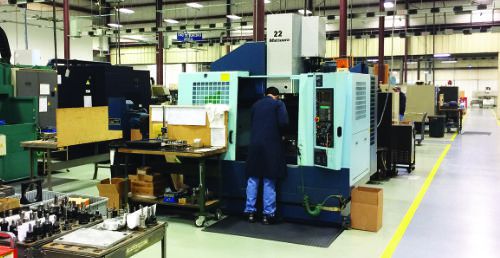
Ron McLeish, Facilities Manager at Paramount Machine, needed a way to keep the coolant clean in his 40+ machines. As an AS 9100 certified shop, Paramount is always looking for ways to reduce its environmental footprint, and recycling coolant was a key component to reducing its overall waste stream. A search for a solution led McLeish to Keller Prod- ucts, provider of metalworking fluid recycling products.
The visit from Paramount’s local Keller representative focused on several larger machines that would use the Keller TKO units to keep them clean. However, McLeish had re- quirements beyond those areas, and was looking for solu- tions to be dedicated to the rest of the machines in the shop. McLeish found that the Keller MB 17-SK Black Magic skim- mer package best fit his needs.
The Black Magic skimmer package incorporates elements that eliminate two classic problems with skimmers: excess coolant removal and messy, overflowing collection buckets. The Keller skimmer package features a cotton felt belt, which is designed to provide enhanced oil removal and durability. The skimmed fluid is delivered to a “Skimallessor” tank, which collects the oil and returns and coolant back to the sump. The entire package is contained in a convenient bracket that is adjustable, and utilizes a magnetic mount for easy installation.
McLeish installed the first skimmer package on a large Matsuura to check the performance. “The results were excellent,” he said. “The sump was clean, and the oil drained from the Keller skimmer was solid oil. It eliminated coolant waste.” A plan was made to purchase enough units, over a period of time, to satisfy the requirements for the whole shop.
As for the benefits of the program, McLeish stated, “If dirty coolant machined better, no one would ever dump it. Keeping the coolant clean yields better tool life, better part finishes, less downtime and less waste. For the cost of these units, the payback is immediate.”
Paramount is a family owned and operated machine shop. “We pride ourselves on delivering quality parts, and recognize the importance of investing in ongoing shop maintenance items to improve performance and keep operating costs down,” said McLeish.
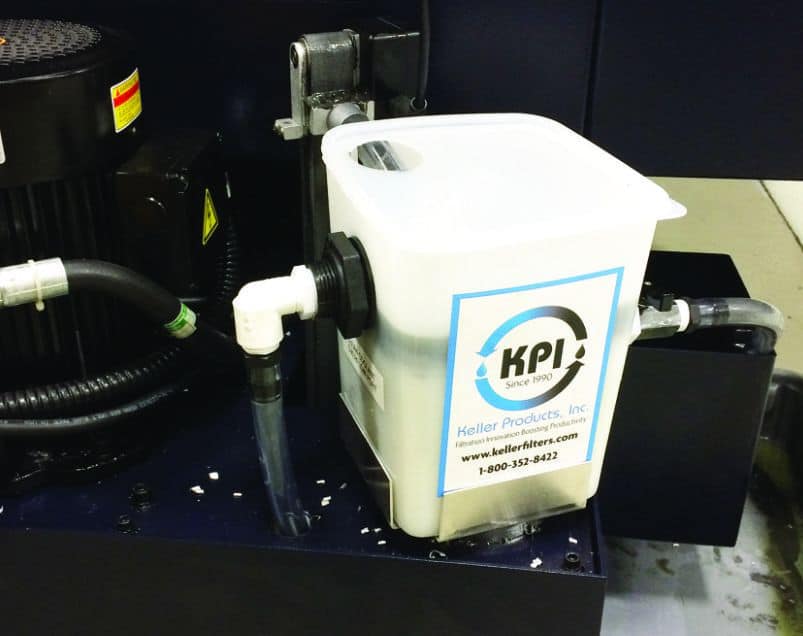
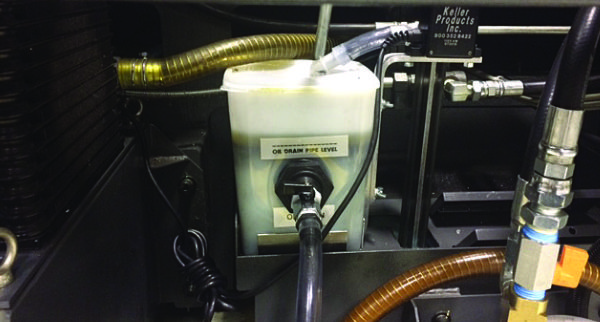